
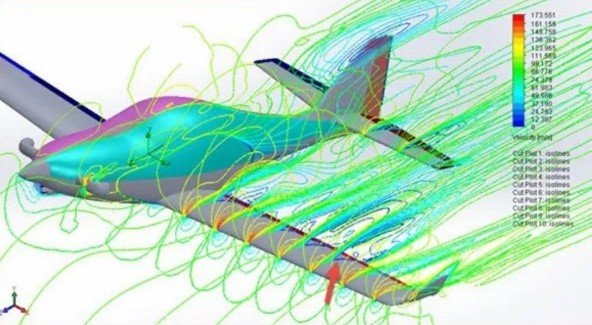
You can simplify and speed up the process by making some drastic assumptions, like assuming the flow is fully laminar (no turbulence), or assuming relatively large CFD elements to lower the size of the matrix, etc. Accurate CFD would require solving the above matrix inversion repeatedly at very small time increments.Ĥ. Turbulent flow is by definition time dependent, meaning that at any given instant those tiny particles of air could be moving in a completely different direction from the previous instant. If I could describe CFD in a single sentence, it is would be a digital algorithm for the inversion of a massive double precision floating point matrix.ģ. For accurate CFD you need many millions of small air particles (mesh elements in CFD) particularly in the close vicinity of the wing leading edge.Ģ. Your much bigger problem is modeling the moving turbulent air around the propeller. It is not difficult to model the geometry in SW - I can gladly help you with that.
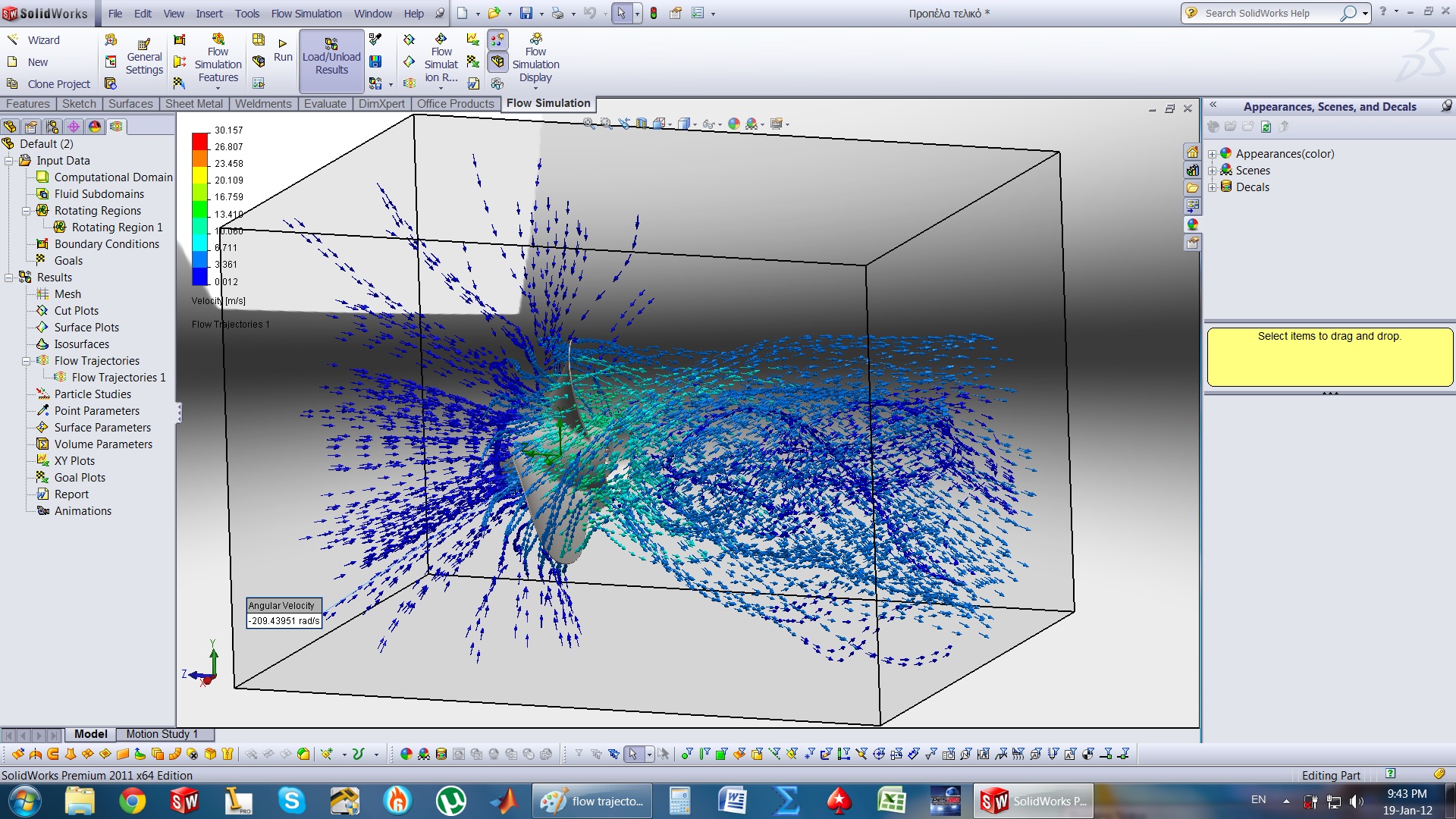
A propeller is a rotating wing with varying airfoil profiles, angles of attack, and airspeed. I like using SW so please don't get me wrong if this post takes the wind out of your sails and enthusiasm ), but I feel the necessity to explain the order of magnitude of the problem you're trying to solve.ġ. My flight sim is a 5900X / 2080 Ti but sounds like that is not going to cut it? Would that be sufficient to model things like designing fiberglass fairing on a wingtip for example (clean air ahead of it). When you say haven't got enough, what hardware would be required to do these analysis in a reasonable period of time (say overnight) assuming the other hurdles could be achieved? A 5990X/3090 is relatively affordable in the context of an airplane. I do see the Premium version has the features I'm looking at using, which is great. I am looking more for "better or worse" rather than explicit accurate values, but maybe there's no way to halfway do this and get any useful data. It doesn't seem like the exact propeller shape would be critical to get at least some useful data. I assume I could find a representative propeller, but I am not sure if the analysis would then be useful in that case. So this would be dependent on a propeller manufacturer sharing their model as well, which now that I think about it seems very unlikely. I do not have the skills to model a propeller by myself (I am totally new to SolidWorks), but there does seem to be a model of a CH 750 available.
